Best environmental investment solution
Rotary Egg Tray Making Machine
2000~6000 PCS/HOUR
What's the egg tray production line
The egg tray machine is the most important equipment in the egg tray production line. If you are struggling with how to deal with a large number of discarded cartons, magazines, papers, and old books, and wondering how to turn waste into treasure, the pulp egg tray production line is a great solution for you.
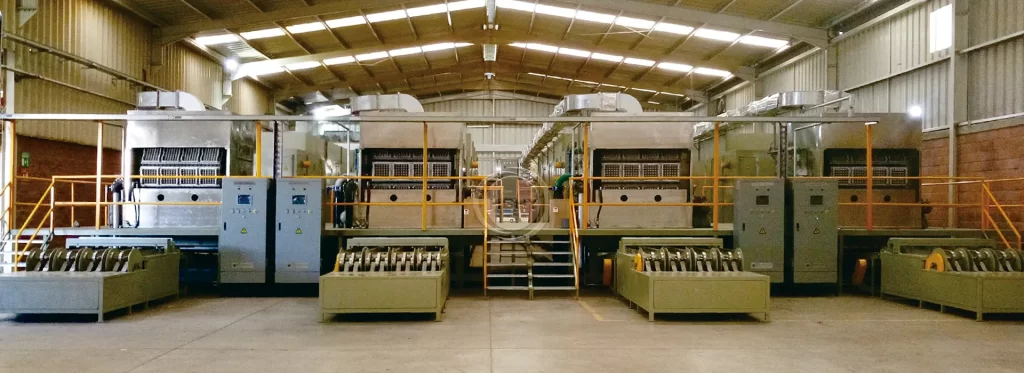
Environmental friendly
Paper egg trays are made from environmentally friendly recycled pulp and fiber pulp. Compared to plastic or other types of egg trays, paper egg trays offer a diverse range of raw materials, superior performance, lower production costs, and significant environmental benefits. For most investors, this represents a promising and profitable business opportunity!
Raw materials
The raw materials used in our egg tray machines are mainly waste paper. There are various types of materials that can be used to make egg trays, such as cardboard boxes, books, magazines, A4 paper, waste paper trays, paper products, cardboard, newspapers, and office paper.
Egg Tray End Product
By changing the mold and adjusting the manufacturing process, HGHY egg tray production line can produce egg trays of various sizes and colors, including goose egg trays, quail egg trays, duck egg trays, pigeon egg trays, and ostrich egg trays. Additionally, the weight of the egg trays can be adjusted according to customer requirements.
Production Process
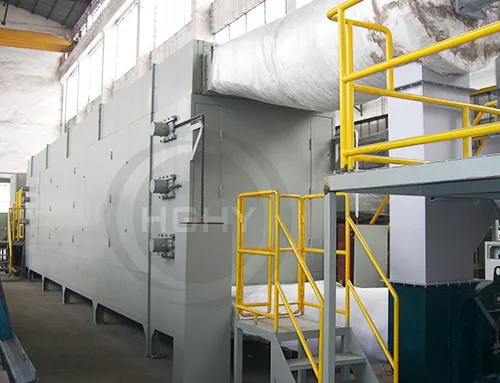
Drying system
Applying sufficient hot air uniformly across the surface of the pulp molding items to eliminate the moisture evaporating from the damp products. Following the drying process, they are directed towards automatic stacking and shrink wrapping for packaging.
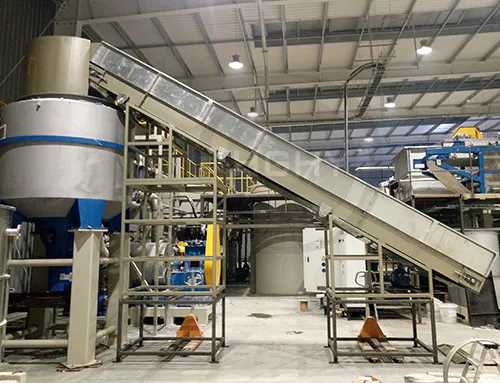
Pulp Preparation System
The process of mixing bagasse, bamboo or wood pulp with water or chemical solutions and processing it into a pulp-like substance
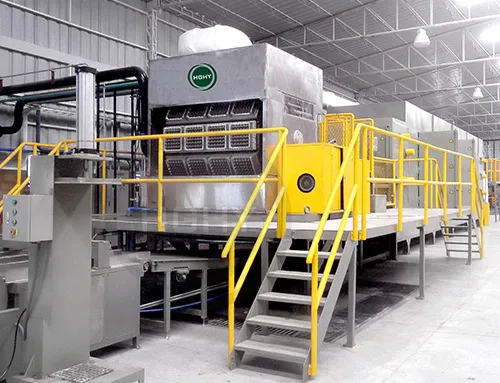
Forming System
The slurry is used to create products through vacuum suction within the forming mold. Afterward, the pulp molded items are transferred using a transfer mold and directed to the subsequent drying line.
Technical Parameters
- Sold out for more than 150 lines
- Rotary forming machine
- Platen Size: 1600*400MM, 1600*560MM, 1950*420MM, 2350*420MM
- Rotary forming machine
- 6 layer dryer
- Rapid Return on Investment, Remarkably Efficient;
- Outstanding Results Achieved Through Rotary Forming Innovation;
- Compatible with a Highly Efficient 6-Pass Drying System;
- Enhanced Product Durability and Reduced Deformation.
Recommanded Model | 2000B1C | 4000B1C | 6000B1C | |
Molding Machine | Rotary Technology | |||
Molding Faces | 4 Faces Forming 1 Face Transfer | 8 Faces Forming 1 Face Transfer | ||
Platen Size | 1600 × 400 mm | 1600 × 560 mm | 1950 × 420 mm | |
Cycle Time | 7.2 seconds | 3.6 seconds | 3 seconds | |
Drops per Minute | 6 Layers | |||
Drying Energy | Diesel / Natural Gas / LPG / LNG etc, or Boiler System of Steam / Conduction Oil | |||
Standard Capacity / Hr | 2,000 pcs | 4,000 pcs | 6,000 pcs | |
Standard Capacity / Day | 48,000 pcs | 96,000 pcs | 144,000 pcs | |
Floor Plan (m) | 50 × 18 × 6 | 60 × 18 × 6 | 72 × 18 × 6 | |
Labor / Shift | 3~4 | 4~5 | 4~5 | |
Raw Material | Waste Paper | |||
Max Product Height | 70 mm |